After stripping. appropriate contacts or wire
end ferrules can be crimped to the end of the cable. Crimping produces a
reliable connection between conductor and contact, and has more or less
completely replaced soldering. Crimping describes the production of a uniform,
nondetachable connection betweem conductor and connecting element. This should
be achieved exclusively by the use of a high-quality precision tool. The result
is a safe, reliable connection in both electrical and mechanical terms. |
|
|
|
Weidmuller offers a wide product
range of mechanical crimping tools. An integral ratchet mechanism with
disengaging option guarantees optimum processing quality. Crimp connections
produced with Weidmuller tools comply with international standards and
specifications. |
|
|
Crimping of wire end
ferrule: Optimum crimp of different cross-sections as an example: |
Examples for the visual
inspection of a crimp connection with manual and automatic crimping tools by
Weidmuller: The conductor insulation must be pushed into the plastic collar.
The ferrule sleeve must be completely filled by the conductor. Depending on the
cross section, the conductor should protrude approx. 0...0.5 mm from the
ferrule sleeve. |
|
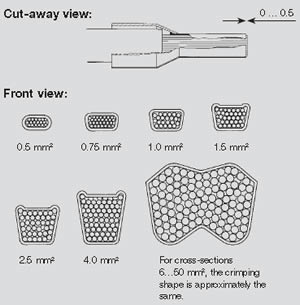 |
|
Faulty
crimping connections due to incorrect combination of cable and wire end
ferrule: |
|
It is not possible for
a tool to function reliably with every combination of conductor and crimping
material. It is possible that the stranded requirements for the crimped product
can't be achieved, although taken on their own, both conductor and crimping
material comply with the corresponding standard. The individual production
tolerances of conductor and crimping material do not allow every conductor to
be combined with every contact. |
|
The combination of
conductors, crimping material and crimping tool must be coordinated: this
procedure is all the more difficult given the large number of products on the
market. This means that the material must be defined and the crimping result
tested, ensuring that the test, and later on the tool, satisfy the same
conditions. |
|
Faults which can occur
during crimping: |
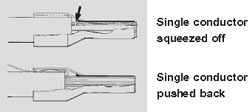 |
- Cracks along the sides and die impressions
- Splitting of the ferrules
- Asymmetrical crimping shape
- Extreme burrs formed along the sides
- Ferrule not filled by the conductor
- Single conductors pushed back protruding from the
collar
- Single conductors squeezed off
- Plastic collar damaged by the crimping jaw
- Conductor insulation not pushed into the plastic
collar
- Ferrule bent longitudinally after crimping
|
|
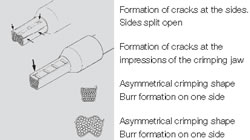 |
|
|